The stock Trailing Arm Bolts (or TABs) are prone to bending, and eventually breaking over time. The solution is to replace them with Toby TABs made from Inconel 718 from DeLorean Parts Northwest. Here’s some of the history behind their development.
This is a nickle-based super-alloy. “Inconel 718 also has a very high fracture toughness, which means that it is very difficult to initiate and propagate a crack. It’s virtually corrosion proof, non-magnetic, and is used in the aerospace industry whenever a failure is absolutely not acceptable (engine mounts, landing gear, and wing attachments, to name a few).”
DMCNews.com has some information (with pictures) about TABs here.
Let’s get started. Supplies used:
- Ratchet and socket set
- 13mm combination wrench
- 3/8th drive 11/16th Torque Adapter
- 3/8th drive Torque Wrench
- 19mm offset wrench
- Crescent Wrench
- Anti-seize lubricant
- Silicone lubricant
- Jack stands
- Low profile jack
- Another jack
- Car ramps
- Wheel chokes
- Utility Light
- Workshop Manual – Section K (Rear Suspension)
- Reciprocating saw (if necessary)
This process of replacing the bolts is relatively easy if you have a manual transmission. I took the following picture from under a lift. Here’s what that area of the frame looks like on a manual car:
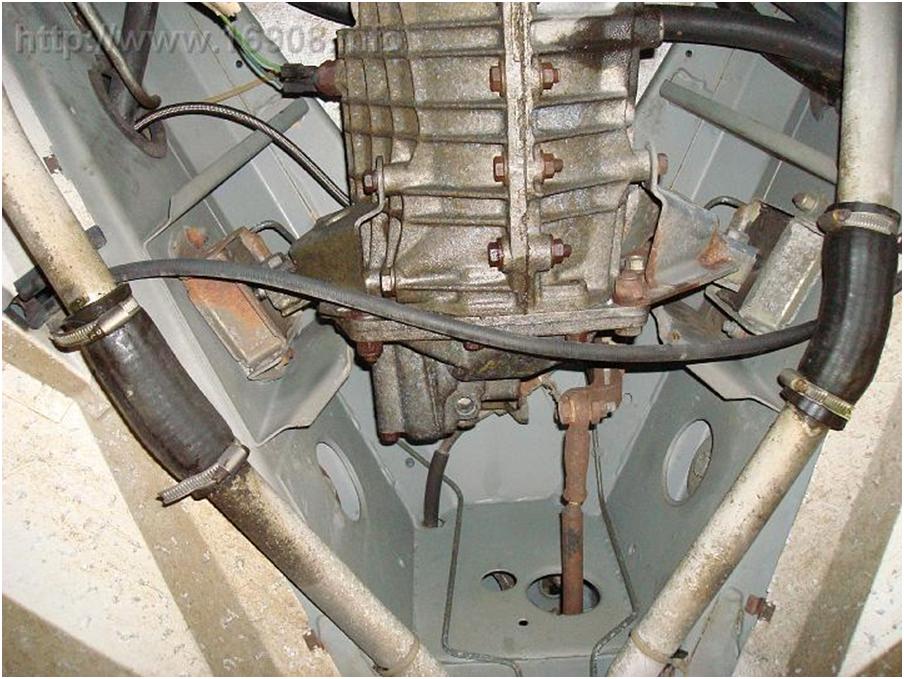
Nice and clean, eh? Alright, here’s the best picture I could get of the same area on my car:
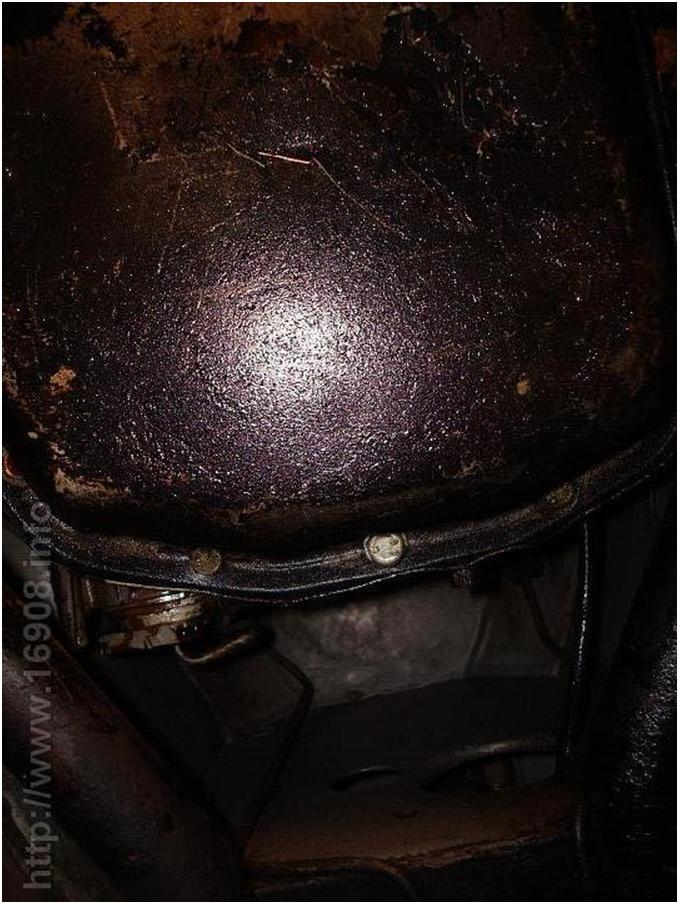
You can see the big ol’ honkin’ automatic transmission almost touches the coolant pipes, and you don’t have access to the nice holes in the frame where the heads of the bolts are located. Argh. Alright, after reading probably every TAB thread on the DML and DMCTalk, I’ve figured out:
- It’s easier to replace the TABs on an automatic car when the transmission is out of the car, or has been lowered out of the way
- You need to remove the trailing arm from the hub carrier on the driver’s side to maneuver the bolt out.
- If a bolt is really bent, you need a reciprocating metal saw to cut it apart for removal.
- It’s way easier to do this with a lift or a mechanics pit
- You need a good offset wrench to hold the heads of the bolts. If you know a good welder, get a cheap wrench, cut it up, and weld a spacer in it.
I don’t have a lift, or a mechanics pit. I have a single car garage, with barely enough room to work. I don’t have a creeper. I can’t get the car higher than 15 inches at the frame with my jack. Maybe worst of all, I don’t have anyone to help me with this job.
Here I go. Jack up the car using the proper procedures, put it on jack stands, and leave the jack in place. Choked the wheels with new wheel chokes. I also used a ramp and 10 lb weights on the driver’s side under the underbody, and an alloy wheel and 10 lb weights on the passenger side under the underbody. There’s about a half inch gap between the underbody and the weights. If the car should fall, this assorted stuff will support it. It gets in the way a lot, but I’m not taking chances… I’m very afraid of the car falling on me. Also notice my foam insulation that I lay on.
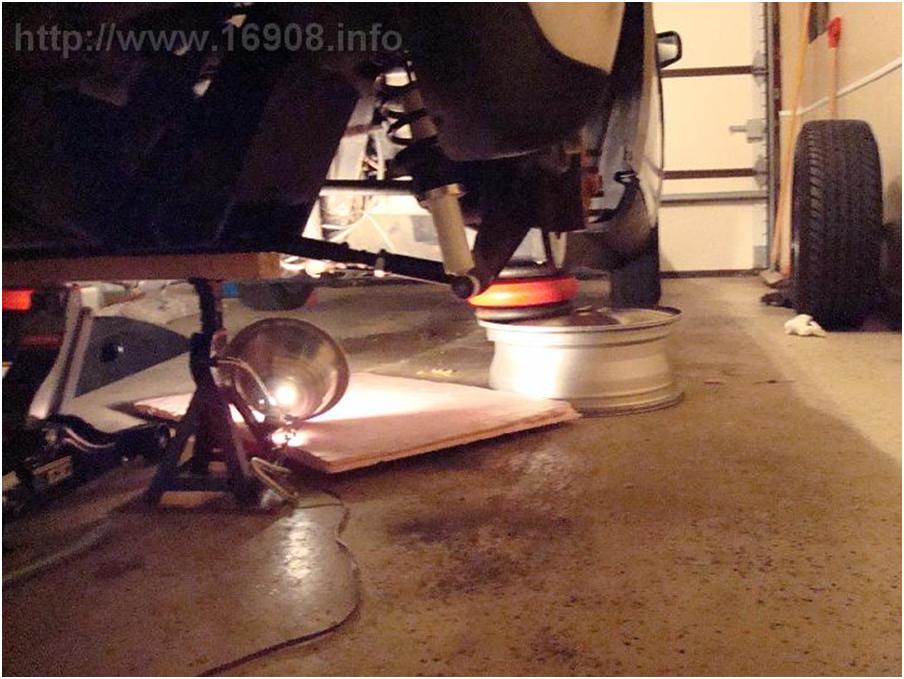
I got a set of metric offset wrenches from AutoZone for this next part:
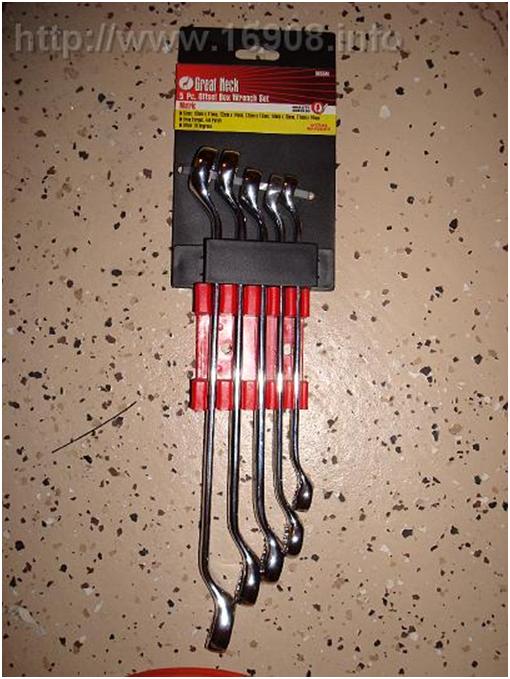
I used the offset wrench to hold the head of the bolt, while removing the nut. I struggled to remove the bolt from the trailing arm. Finally I used a flat screwdriver to push on the threads of the bolt. Once it was out of the trailing arm, I pushed the bolt back into position, with the trailing arm below the bolt. I started removing the plate that holds the bushing in place:
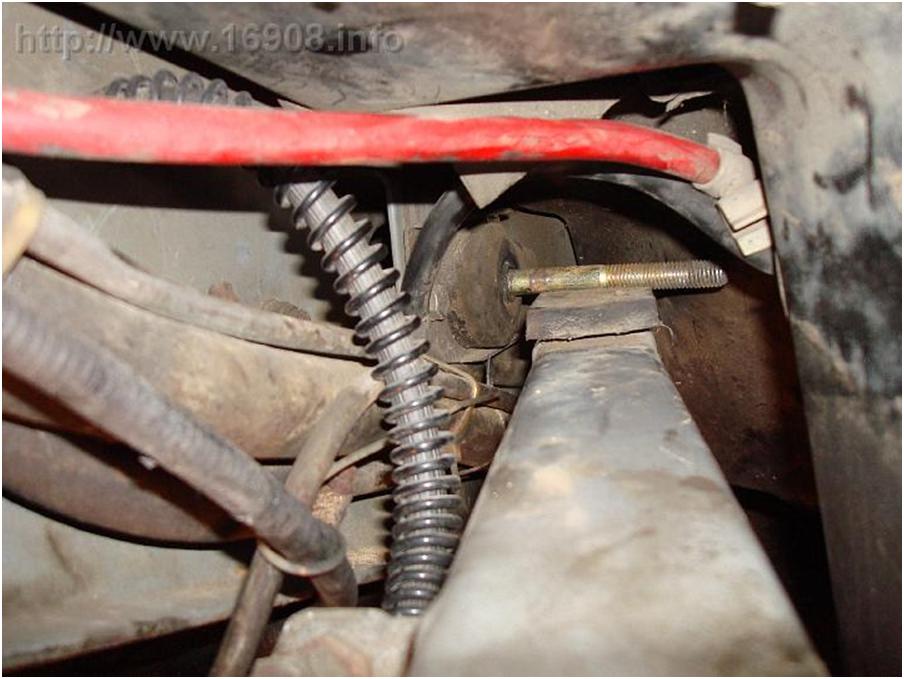
After I struggled with the reinforcing plate bolts for a few hours, I finally got it off! The bolt is free! Here’s what all this stuff looks like:
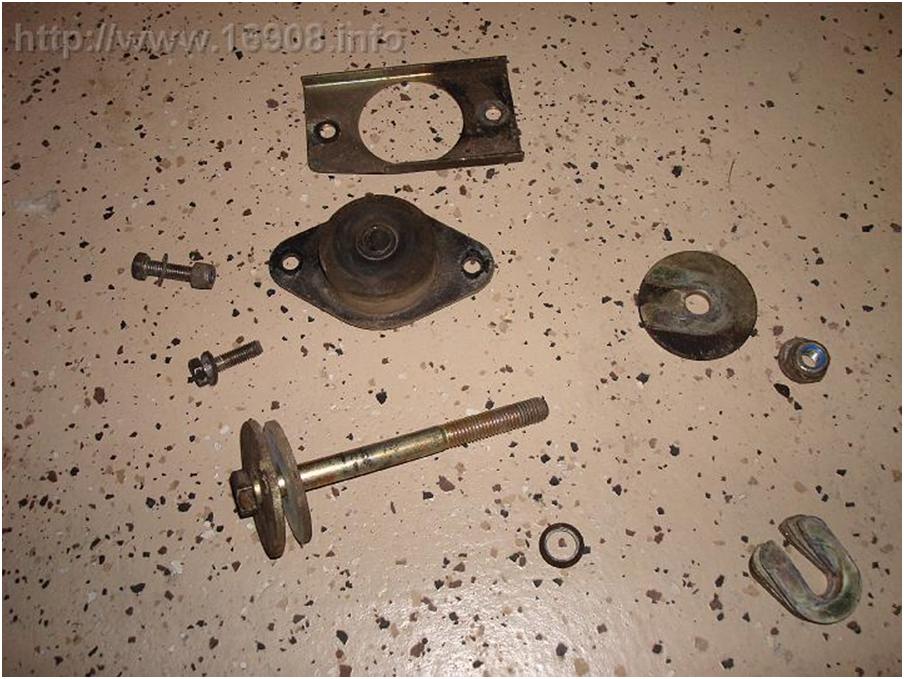
I lost a jam nut, but found it a few days later. Which brings me to:
Helpful Tip #1: Tape the ends of the recessed are of the frame. The jam nuts will fall and roll out unless you’ve got something to catch them. The tape will catch them.
Here’s the moment of truth. Take a close look! All my effort was not in vain! The stock TAB is bent!!!
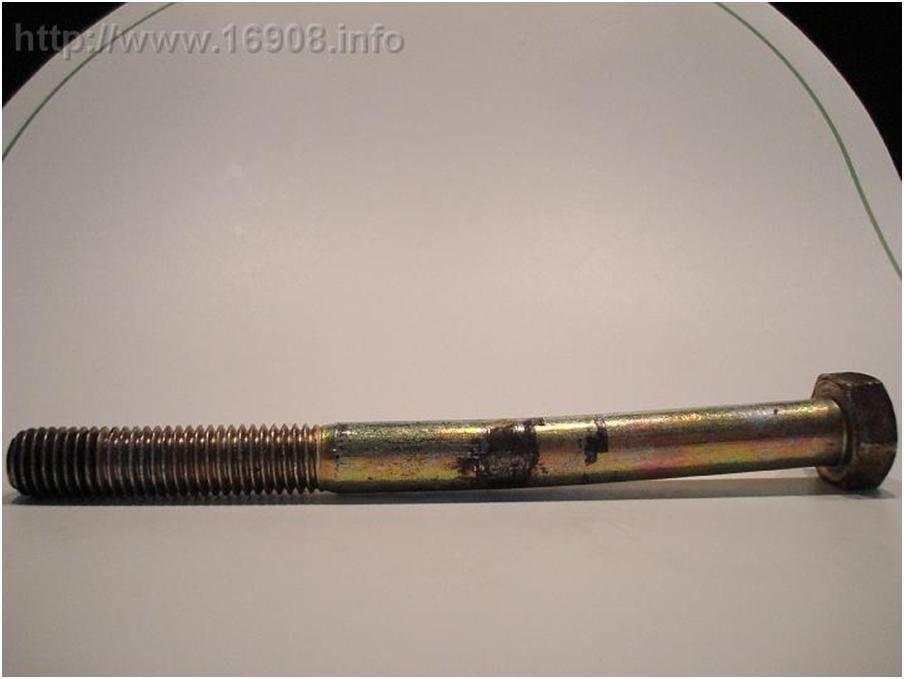
I cleaned the parts, used some silicone lubricant to “treat” the bushing, and some anti-seize on the bolt. Here are all the pieces cleaned, ready for assembly:
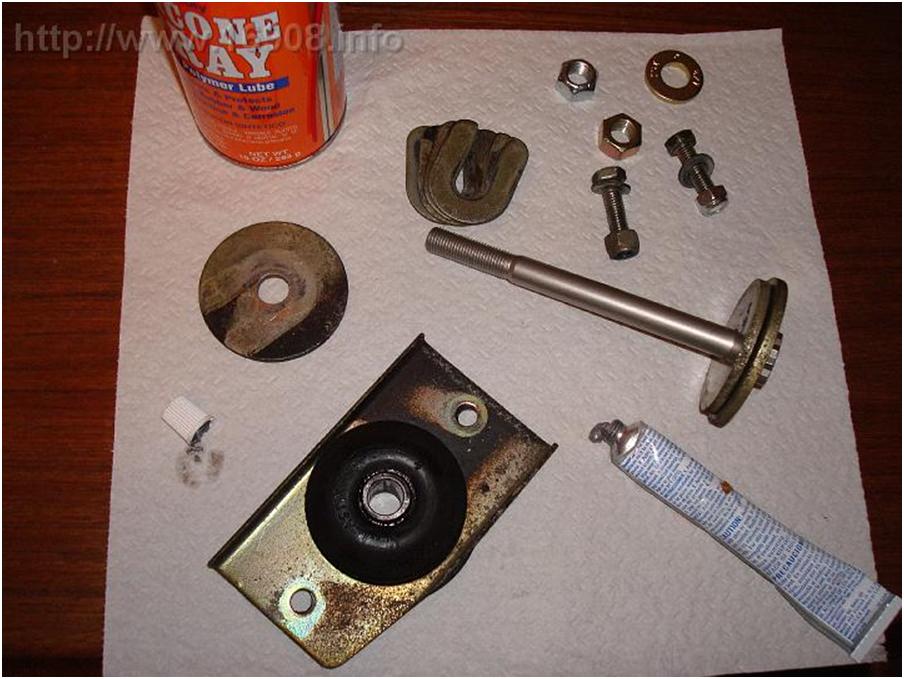
Now, I thought of a way I could hold the jam nuts in place, in such a difficult, small area.
Helpful Tip #2: Hammer the end of a small wire tie into the lock nut: The wire tie is small enough, and flexible enough to fit into the recessed area of the frame. Once the bolt catches the nut, rip the wire tie out.
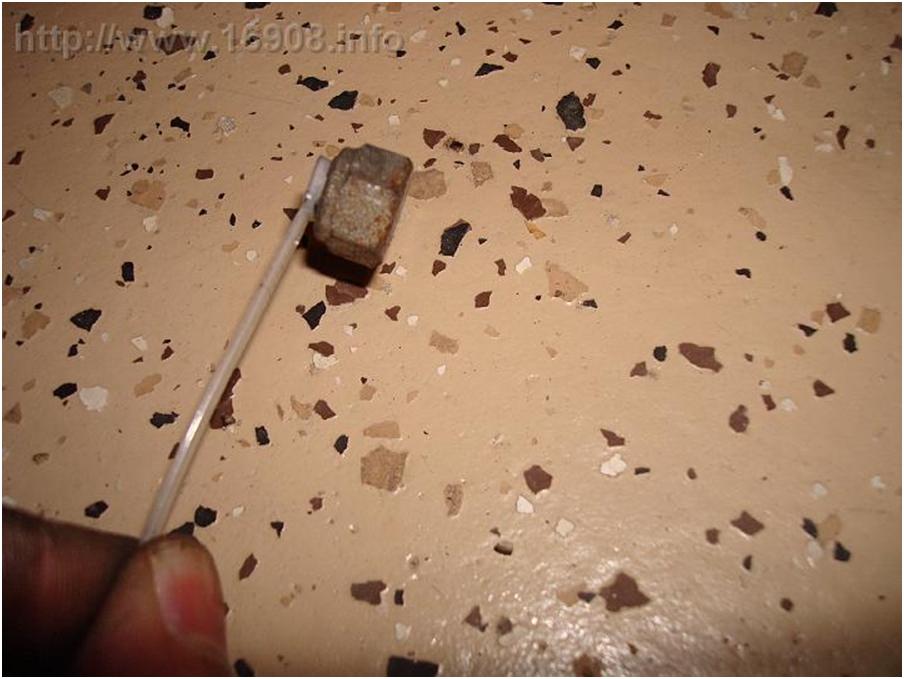
Helpful Tip #3: Don’t use a closed end combination wrench on the 13mm nuts. You won’t be able to get the wrench off once the bolt is in. Use an open end combination wrench.
Once I got the retaining plate mounted, I struggled to reinsert the bolt into the trailing arm. The mess of cables and hoses on the driver’s side makes everything more difficult:
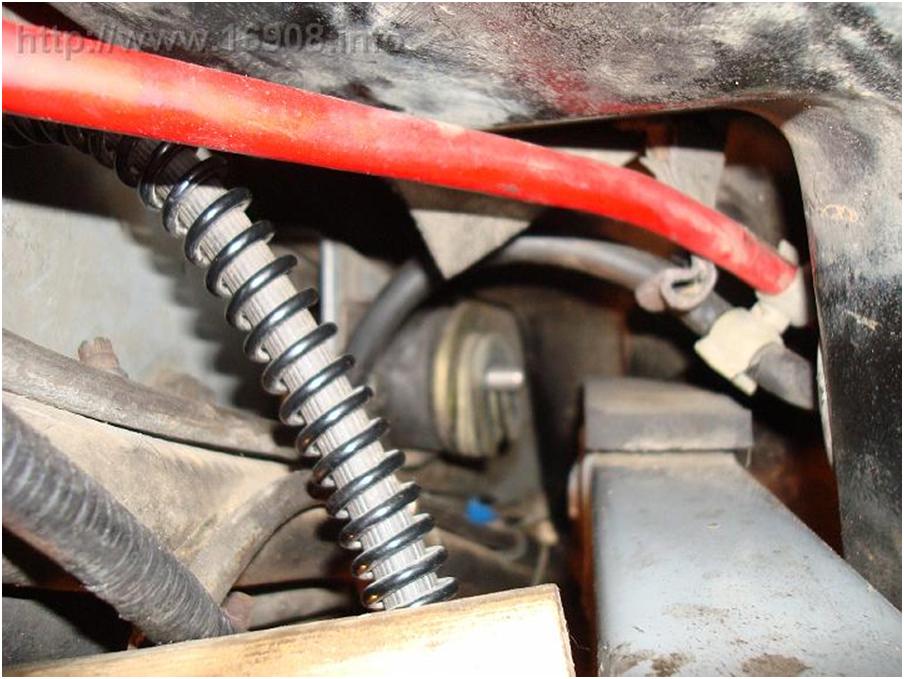
I realized the trailing arm was in a position that made this task impossible. So I figured out…
Helpful Tip #4: Jack up the hub carrier about ¼ to ½ inch for bolt removal and reinsertion.
Once the trailing arm was positioned better, the bolt slid in easily:
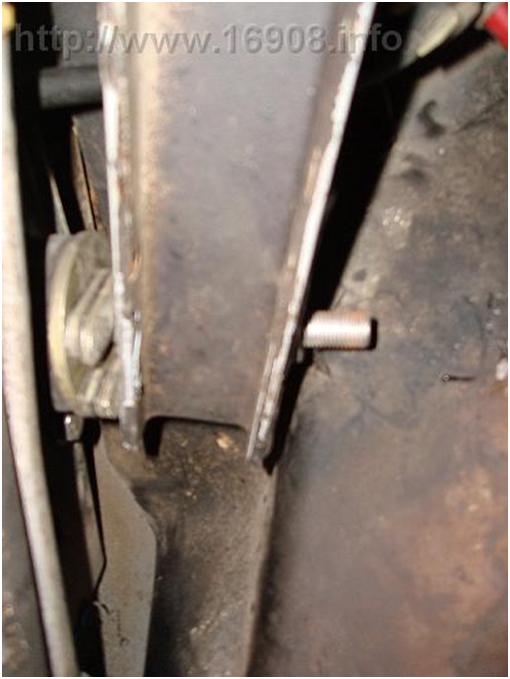
The threaded ends on Toby TABs are tapered down to 18mm. The space is too tight to fit a ratchet and socket. I found an 11/16ths is a good match for 18mm, so I purchased an 11/16ths torque adapter specifically for this job:
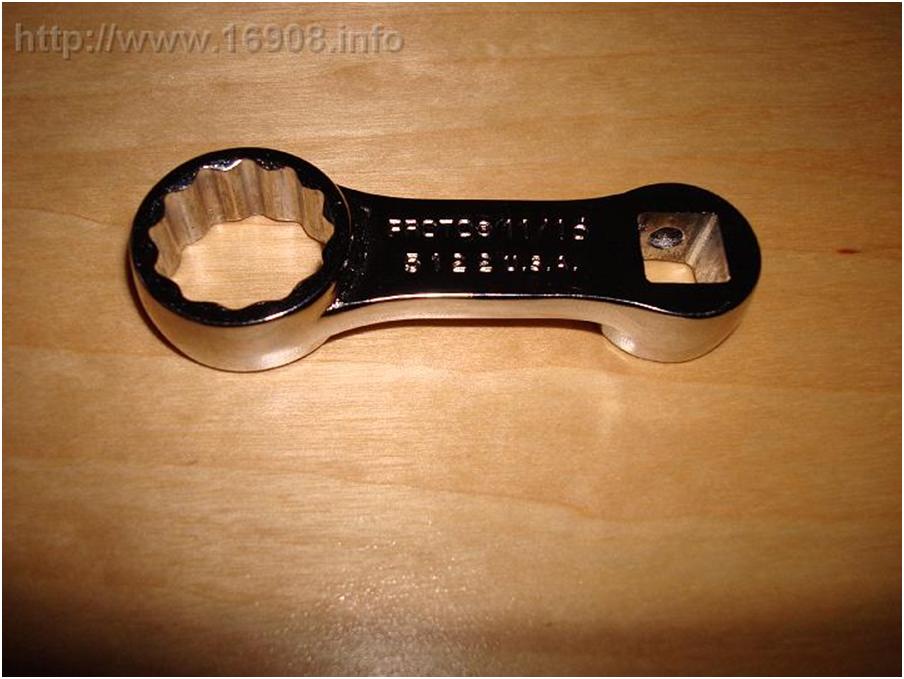
I used it with a ratchet to snug up the bolt
Helpful Tip #5: Use a 18mm Ratcheting Combination Wrench for this job:
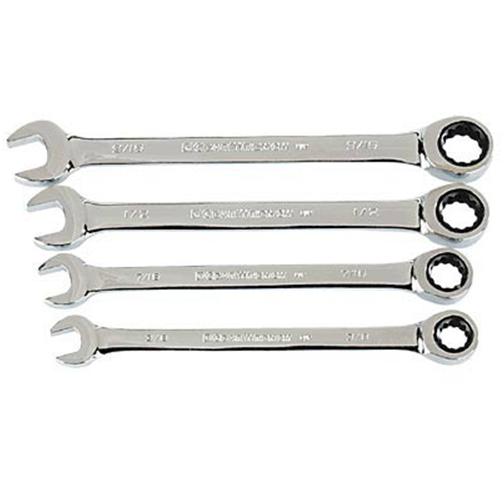
I should have bought one, but I made due with the constant turning of the torque adapter. My arms are tired…
Holding the head of the bolt with the offset 19mm wrench:
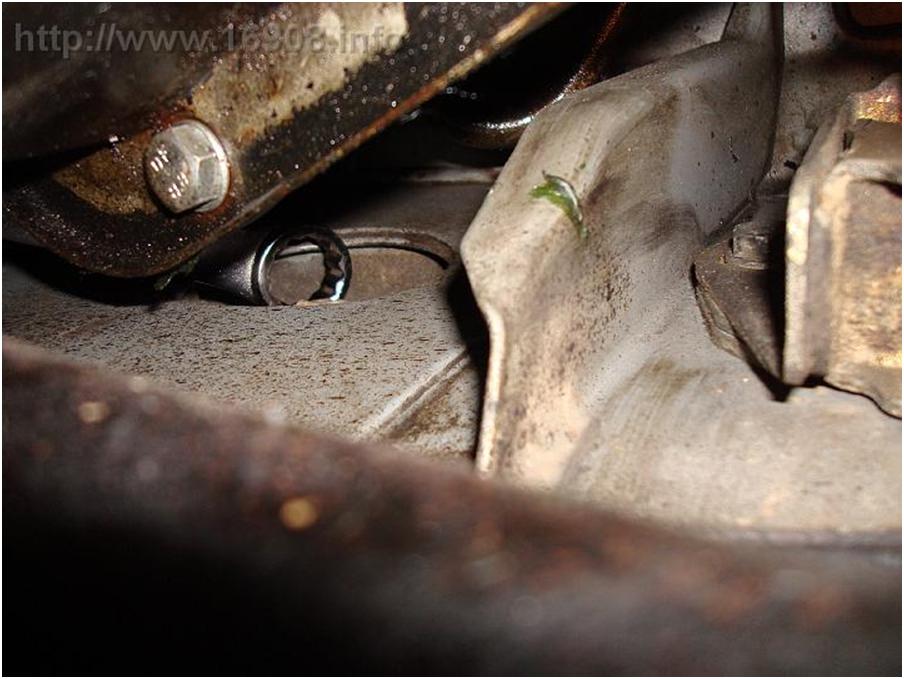
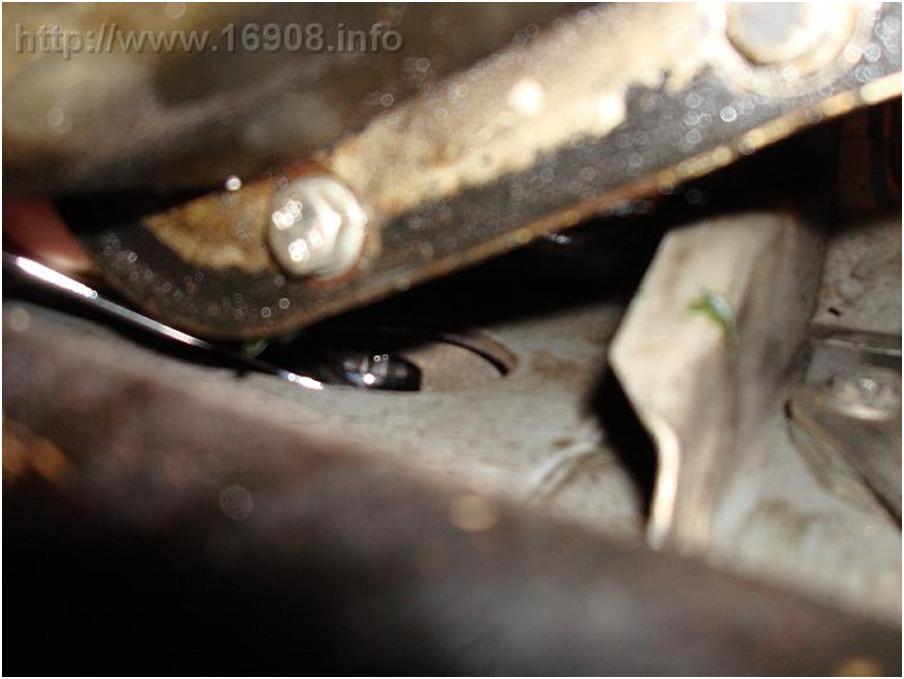
Tightening the nut with the ratchet and torque adapter:
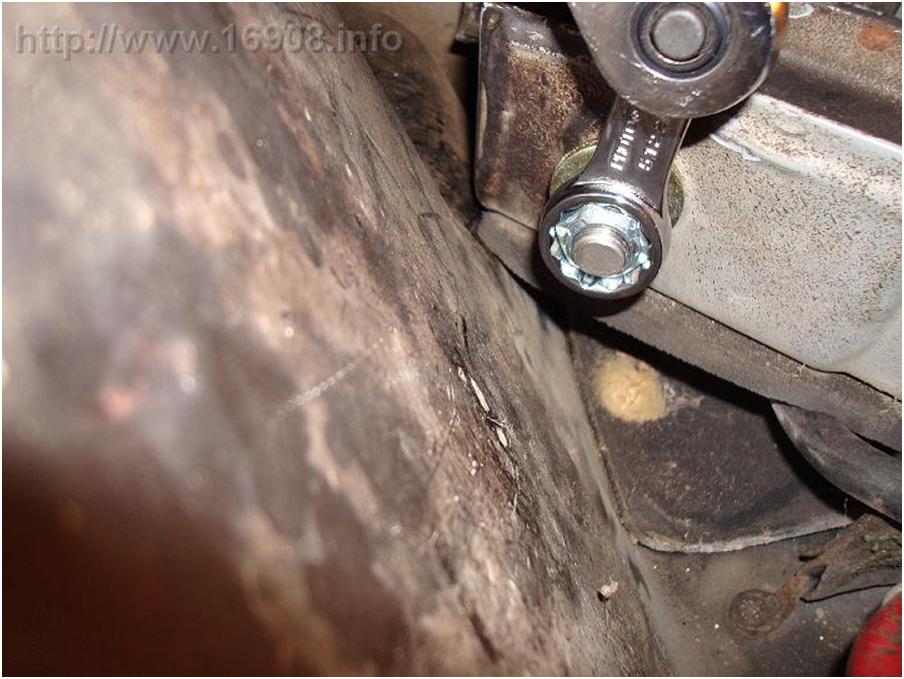
You need to torque the bolts with the weight of the car on the suspension. Supposedly the best results are attained on a level surface. As I said, I don’t have a lift, or pit, so I’ll settle for ramps. Once the nut was snug, I reattached the wheel, lowered the car, and backed it up my ramps. I torque the nut to 53 FT/Lbs with my new 3/8 drive torque wrench:
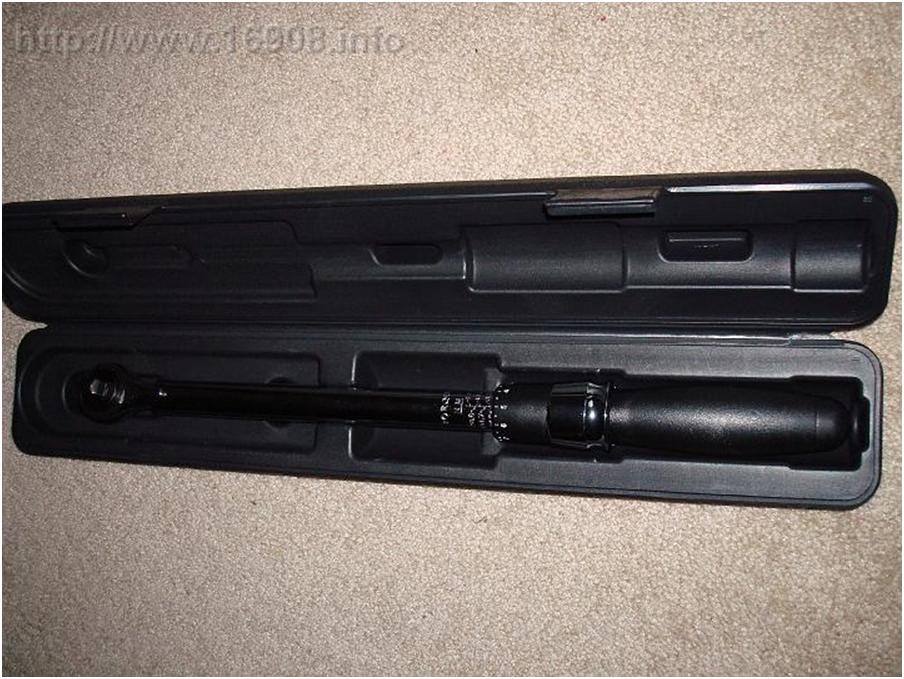
I used the torque adapter positioned perpendicular to the wrench (so to not affect the torque setting). The wrench is a little over 16 inches long, so it was short enough to work with under the car. The passenger side is now done!
Onto the dreaded driver’s side trailing arm….
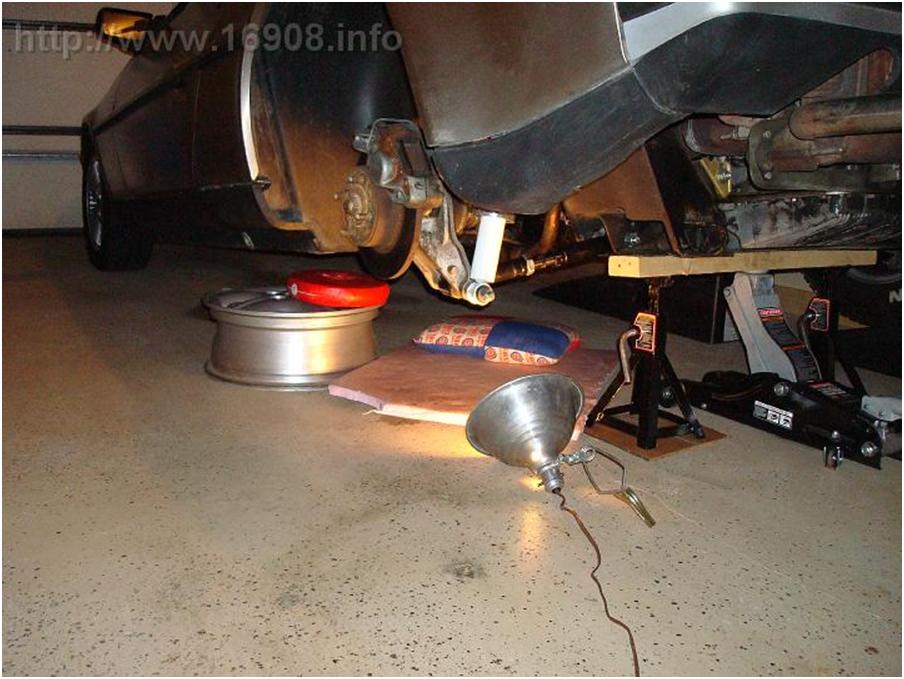
It’s different for the driver’s side process, because you have to detach the trailing arm from the hub carrier to maneuver the bolt out and back in. I wanted to prove this wasn’t necessary, but I found it is…
Supporting the hub carrier for bolt removal (got brave, and used my low profile jack):
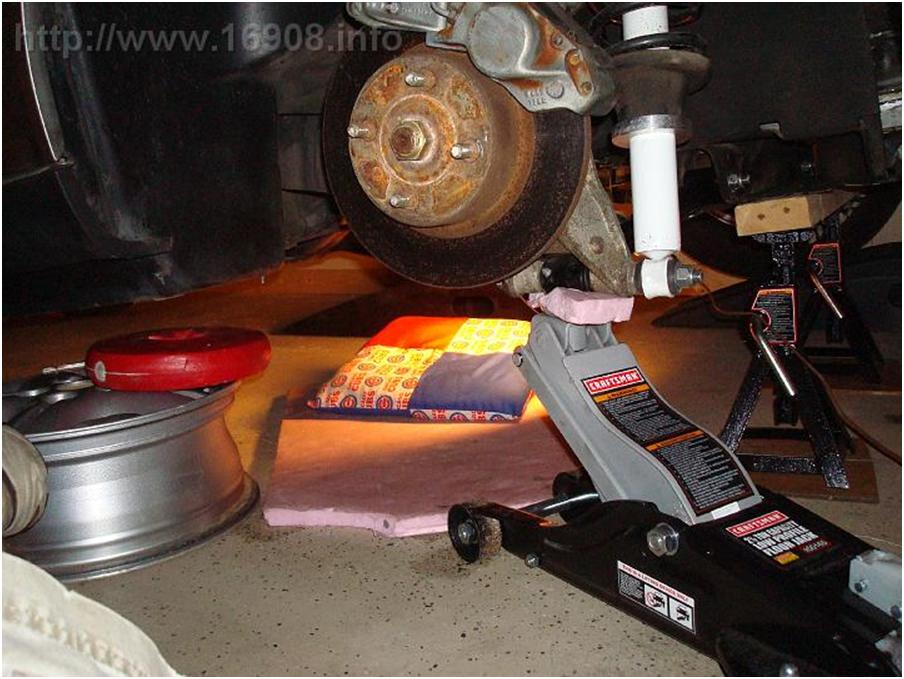
Removing the trailing arm from the hub. First time separated since assembly in Ireland?
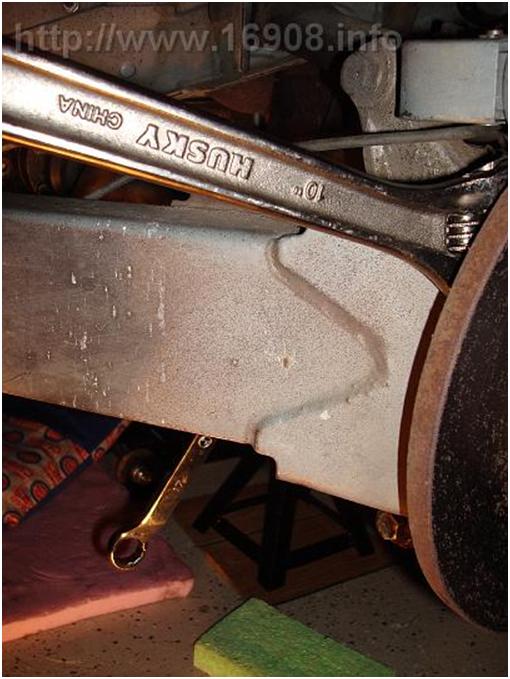
I made sure to be careful with the hard brake line. It will flex, but make sure it doesn’t cause a bend in one location. I was worried the trailing arm would have the weight of a steel beam, and come crashing down. I was relieved to find it’s not very heavy. To get the bolt out, I had to pull the arm away from the hub carrier, and then lower it below the carrier. I put my low profile jack back in place. I borrowed a scissor jack from another car to support the trailing arm, and lower it slowly:
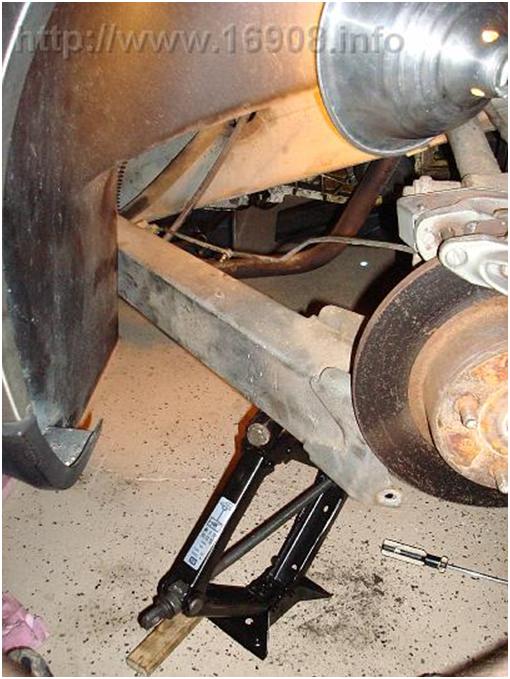
I got the bolt out! The bolt wasn’t as bent as the passenger side bolts, but still slightly bent.
Some cable towards the narrow end of the trailing arm will support the arm:
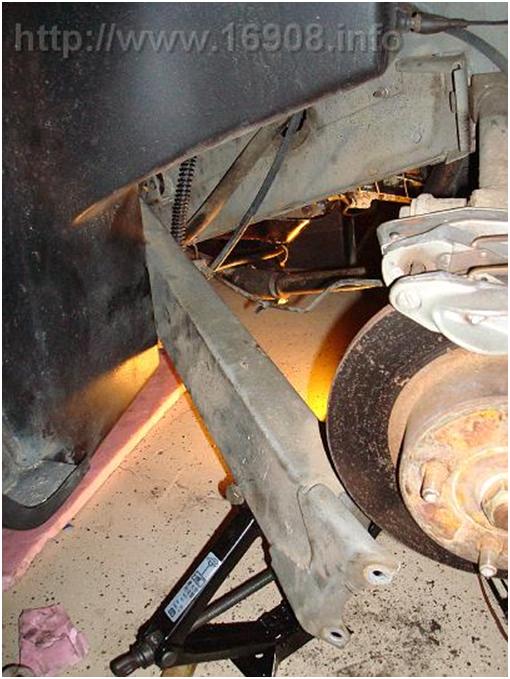
Now I put the new bolt in, started a few threads on each bushing plate bolt, leaving it all loose. I then pulled the hub carrier back, and put the trailing arm back in position. Bolt the trailing arm back up to the hub carrier, and snug up the bushing plate bolts. Finally, snug up the TAB nut.
One last picture before final torqueing:
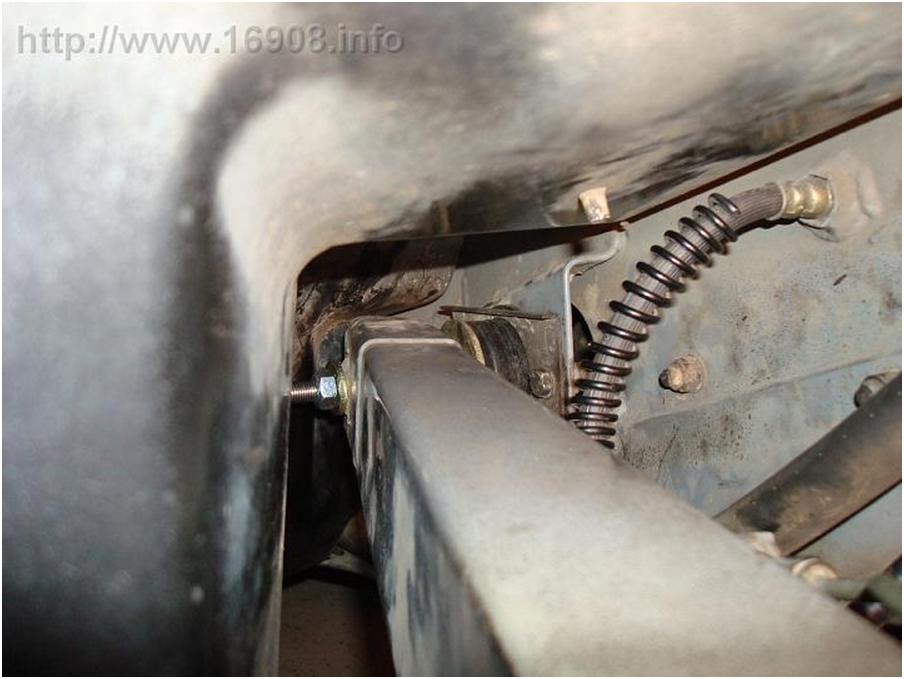
Beautiful, eh?
I reattached the wheel, lowered the car, backed up my ramps, torque the nut to 53 FT/Lbs, and the job was done! I don’t want to do this job again anytime soon…
Time elapsed: 10 days. Mainly because I didn’t know what I was doing. There was a lot of trial and error, and scheduling conflicts. I almost gave up right away, figuring I’d have DMC (Midwest) do this job for me. But I persevered, and continued to accomplish one task at a time. I learned a lot, and I’m pretty damn proud I did this all by myself. I could probably get the job done in a day or two knowing what I know now.
Since I had such a hard time figuring this all out, I felt brave and made two videos. The first is on the bolts themselves, and the second is on bolt replacement with the automatic transmission. Hopefully I didn’t make any mistakes, but please point them out if I did.
Video 1
Video 2
I’m gonna go degrease my hands for the umpteenth time
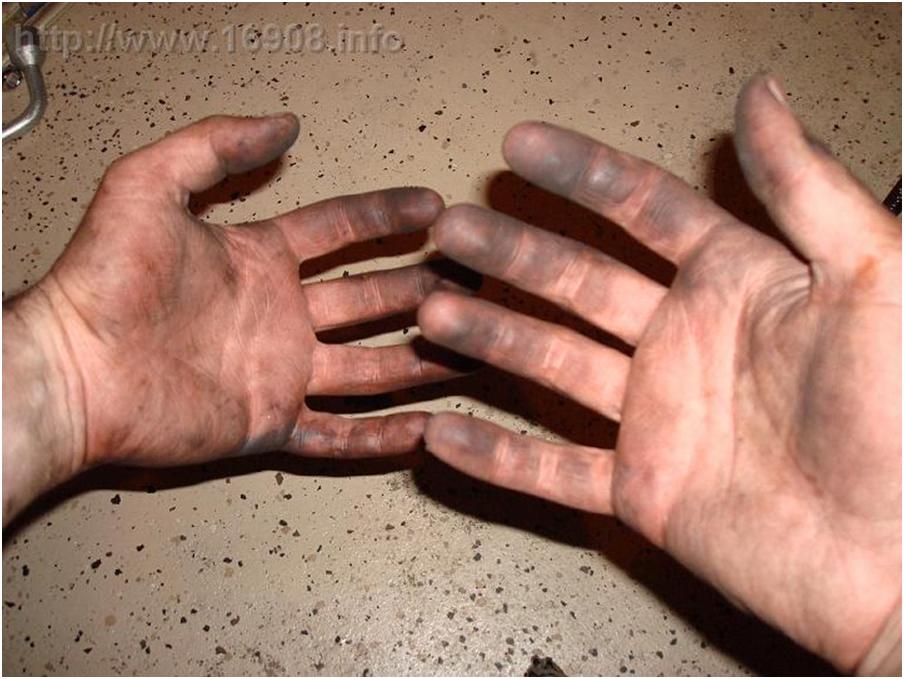
Costs:
K1000DP – Toby TAB Custom Trailing Arm Bolt Kit from DeLorean Parts Northwest – $74.95 plus $4.60 shipping
Proto 5122 Torque Adapter 11/16′ 3/8′ Drive: $15.75 plus $4.98 shipping at Drillspot.com
13mm Combination Wrench: $4.88 plus tax at Menards
Double Box End Offset Wrench Set: 15.99 plus tax at AutoZone.
Husky 3/8 Drive Torque Wrench: $68.96 plus tax @ The Home Depot